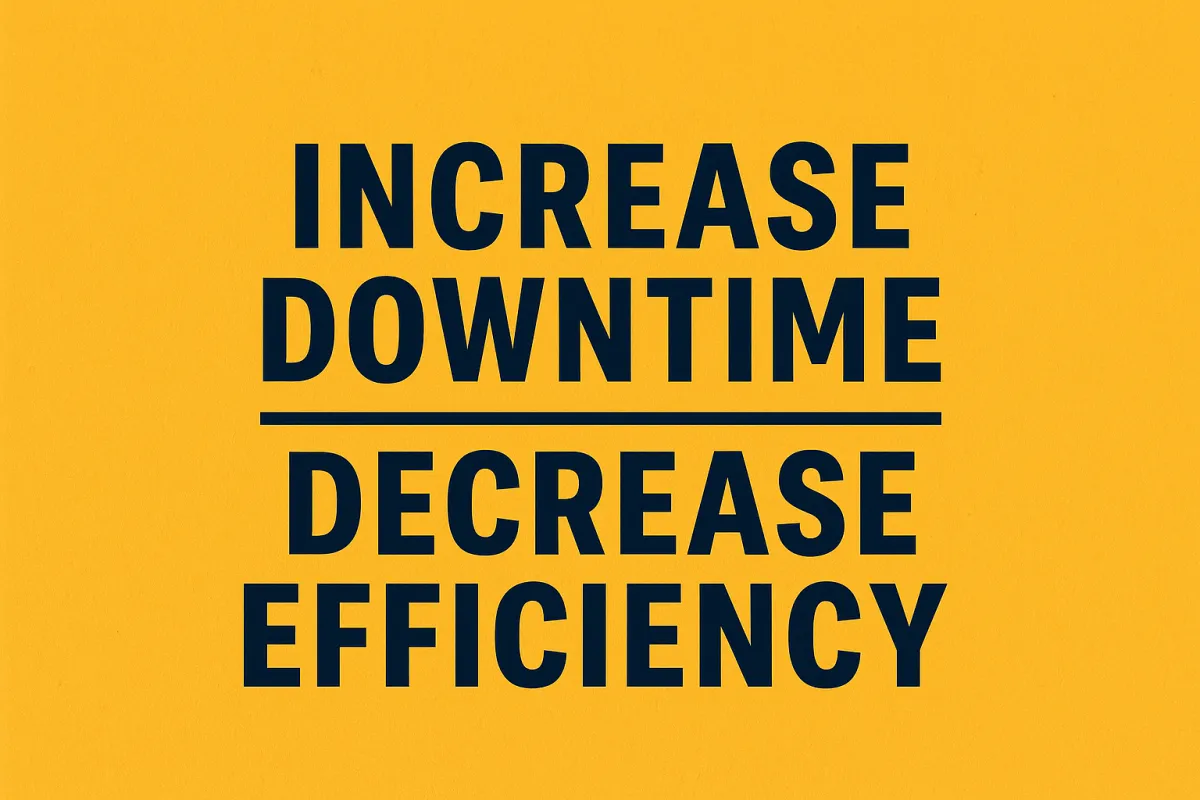
Want More Downtime and Less Efficiency? Do These 2 Simple Things
If your goal is to drive downtime through the roof and slowly chip away at your plant’s productivity, we’ve got great news.
There are two time-tested, rock-solid strategies that virtually guarantee you'll fall short of your maintenance and production goals:
1. Don’t train your maintenance team to troubleshoot.
2. Don’t hire the right people.
Seriously, it works every time.
Let’s break it down, step by step—so you can avoid productivity like a pro.
1. Don’t Train Your Maintenance Team
Want to watch a production line sit still while your technicians stand around scratching their heads? Simple. Just don’t train them.
No structured curriculum. No hands-on learning. No clear process for troubleshooting. Just let them “figure it out” when something breaks. That’s real-world experience, right?
Here’s why skipping training is such a reliable way to increase downtime:
They’ll guess.
With no structured foundation in schematics, multimeter usage, or component testing, your team will rely on trial-and-error—and error, and error again.They’ll part swap.
When you don’t understand the system, just start swapping parts until something works! Sure, it drains your spare parts budget, but hey, who’s counting?They’ll call for help.
OEM support calls, specialist visits, and 12-hour delays are just part of the fun. Nothing says “we’ve got this under control” like paying $8,000 for someone else to diagnose a bad relay.They’ll lose confidence.
And why wouldn’t they? If every breakdown is a mystery and every fix is a coin toss, confidence plummets—and so does morale.
So if your dream is a high-cost, low-efficiency operation? Just keep doing what you’re doing and don’t train anyone.
2. Don’t Hire the Right People
Let’s say someone retires or leaves. You could replace them with someone eager to learn, mechanically inclined, and ready to grow into the role…
Or you could hold out for the “perfect” technician who already knows it all and is magically available at your pay rate.
Spoiler alert: they’re not.
So instead, you do what so many do: stretch your current team thinner, compromise on quality, or delay hiring altogether. And when you do hire, forget attitude or aptitude—just pray they’ll somehow absorb knowledge through osmosis.
This strategy delivers a variety of delightful outcomes:
Overworked senior techs.
Your best people will do everything, while also trying to mentor the underprepared. Bonus points if they leave because they’re burned out.Massive knowledge gaps.
Because without any development plan, those new hires will never level up. They’ll stay stuck in “what do I do now?” mode for years.Team turnover.
People leave when they’re unsupported or feel like they’re set up to fail. Untrained techs leave because they’re frustrated. Trained techs leave because they’re overwhelmed. It's a win-win… for chaos.
Bonus Tip: Combine Both Strategies for Maximum Chaos
Want to supercharge the dysfunction? Don’t train anyone AND don’t hire anyone worth training.
Let everyone learn “on the fly,” only when something breaks. Rely on your one senior tech for everything. Keep calling in outside support. Hope that your budget can keep up.
It’s the fastest way to sabotage efficiency, run up your costs, and stay stuck in reactive mode—forever.
Or… You Could Try Something Different
All jokes aside, the truth is: these two bad habits are the reason so many operations struggle with downtime, high costs, and unreliable teams.
But here’s the good news:
✅ You can train your current team—even the newer techs—to troubleshoot effectively.
✅ You can hire for attitude and develop the right skills internally.
✅ You can build a team that fixes issues the first time and keeps the operation running.
The key? A proven system that combines:
Foundational, step-by-step training
Hands-on learning with real-world application
Expert mentorship and coaching
Built-in accountability and progress tracking
That’s exactly what our Apprentice to Pro Troubleshooting Training Program delivers.
We help maintenance leaders like you train and develop a confident, self-sufficient team in just 12 weeks—without disrupting operations.
Final Thought
If you’re tired of being stuck in a cycle of part swapping, downtime, and guesswork, it’s time to stop doing the same things that got you there.
Don’t settle for chaos.
Train the team. Hire for attitude. Build the kind of maintenance department your operation actually needs.
Looking for more insights on why so many teams stay stuck in reactive mode? Be sure to read our post:
👉 The Reactive Training Trap: Why Most Techs Struggle with Troubleshooting
And if you’re ready to take control of your training strategy, check out our guide on:
👉 Bridging the Skills Gap in Maintenance: Why Training Is the Only Way Forward